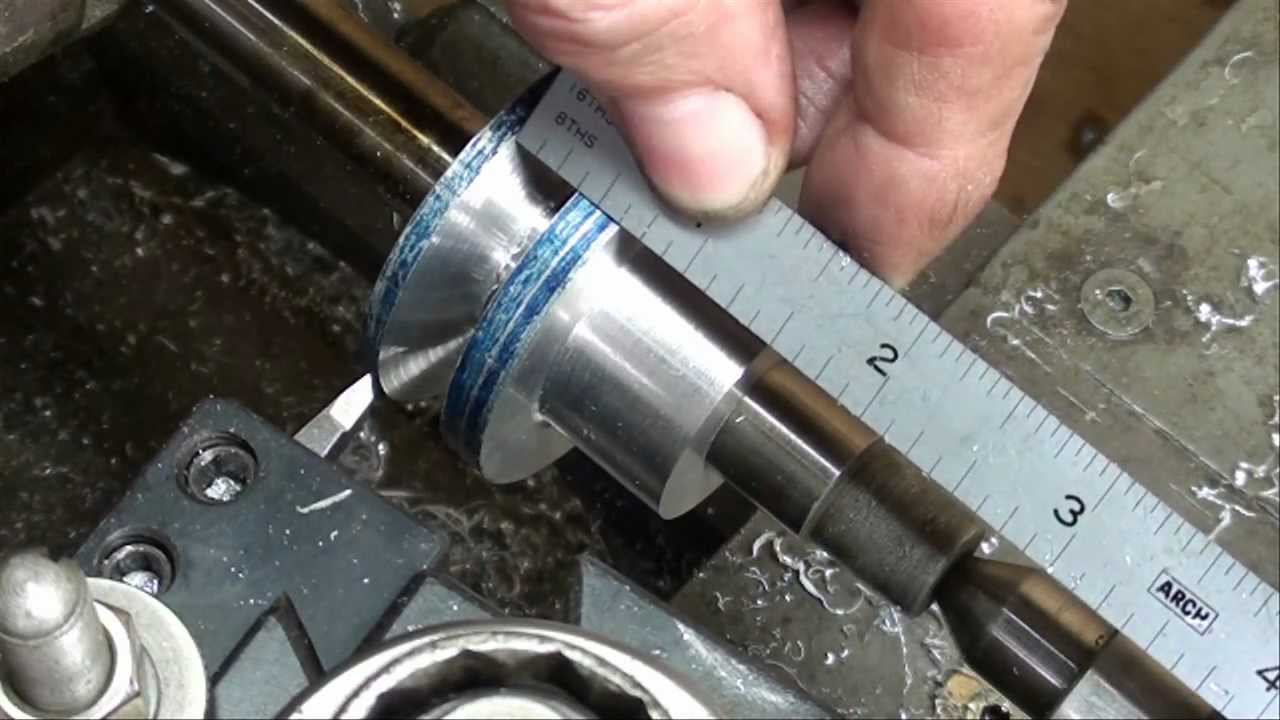
Lathes can be divided into three types for easy identification: engine lathe, turret lathe, and special purpose lathes. Some smaller ones are bench mounted and semi-portable. The larger lathes are floor mounted and may require special transportation if they must be moved. Field and maintenance shops generally use a lathe that can be adapted to many operations and that is not too large to be moved from one work site to another.
The engine lathe (Figure 7-1) is ideally suited for this purpose. A trained operator can accomplish more machining jobs with the engine lathe than with any other machine tool. Turret lathes and special purpose lathes are usually used for any type of lathe work. Further reference to lathes in this chapter will be about the various engine lathes.
basic engine lathes are usually used in production or job shops for mass production or specialized parts, while basic engine lathes are usually used for any type of lathe work. Further reference to lathes in this chapter will be about the various engine lathes. materials. Unlike conventional optical grinding, complex aspheric surfaces can be machined easily.
Instead of the dovetailed ways used on the tool slide of a metal-turning lathe, the ways typically float on air bearings, and the position of the tool is measured by optical interferometry to achieve the necessary standard of precision for optical work. The finished work piece usually requires a small amount of subsequent polishing by conventional techniques to achieve a finished surface suitably smooth for use in a lens, but the rough grinding time is significantly reduced for complex lenses.
Lathes can be divided into three types for easy identification: engine lathe, turret lathe, and special purpose lathes. Some smaller ones are bench mounted and semi-portable. The larger lathes are floor mounted and may require special transportation if they must be moved. Field and maintenance shops generally use a lathe that can be adapted to many operations and that is not too large to be moved from one work site to another.
The engine lathe (Figure 7-1) is ideally suited